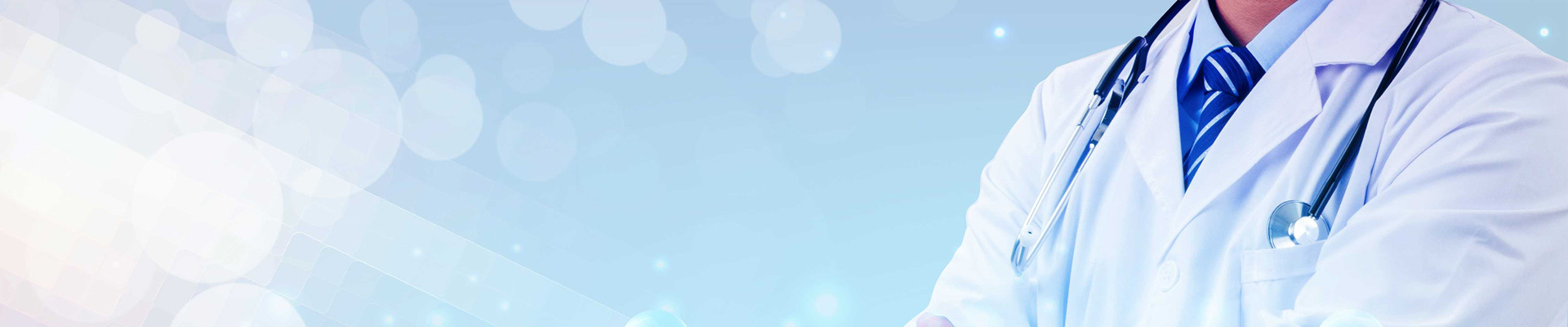
Limitations of online CT detection of power batteries
2023-09-26 10:00As the demand for lithium batteries continues to grow, their production and safety standards urgently need to be improved, so high-resolution, high-throughput 3D inspection systems are essential. Whether the goal is to increase production, improve yield, or shorten production cycles, a one-second CT scan has the potential to revolutionize industry standards for defect detection.
The prospect of a 3D CT scan
Industrial computed tomography (CT) can collect a large amount of valuable data. By generating a complete 3D reconstruction of the internal structure of the battery cell, a comprehensive visual analysis of the internal structure can be performed, allowing for more accurate identification of defects that may affect the function or safety of the battery. Extensive measurement data such as part alignment, thickness uniformity and curvature control are also available to ensure compliance with design and production specifications.
Eliminate common battery defects
Unlike traditional 2D inspection, 3D X-ray imaging provides complete 3D data of the entire battery cell. This is illustrated by two common failure modes: pole-plate alignment and particle foreign matter contamination, both of which cannot be accurately detected by traditional 2D imaging.
1, pole plate alignment
Pole alignment is a key parameter to ensure battery safety. Poor alignment is likely to cause failure during the battery's lifetime. Unfortunately, traditional 2D detection systems do not provide enough information to correctly measure the polarity of the entire unit.
The following figure shows the ability of the CT system to detect the alignment of the intersecting pole film. Liquid metal X-ray sources can acquire a full 3D scan in a second or less, making the technology ideal for in-line and end-of-line inspection during high-volume production.
2. Particle pollution
The presence of foreign debris, such as particles or metal contaminants from previous manufacturing steps, can both hinder the proper charging of the battery and pose a potential safety risk. CT inspection can identify these contaminants to target the cleaning and maintenance of related equipment that may lead to the introduction of debris into the battery cell.
Towards a new standard for battery inspection
Battery manufacturers face challenges in maintaining quality while continuing to scale up production. High-speed online CT inspection can accurately detect defects, facilitate quality control, and provide important data on the integrity of the manufacturing process and the final product, thus playing a vital role in the extremely high capacity requirements and high quality control of today's market. The next generation of CT inspection systems, equipped with high-resolution, high-brightness X-ray sources, will provide an unprecedented amount of inspection data, providing a safer and more promising future for battery manufacturers and their consumers.